作業床が落下する危険要因は幾つかあります。その要因は明確な構造設計,徹底した品質管理,定期的な保守点検を行うことで排除されます。
しかしながら,機械の事故においては,「ヒューマンエラー」を含む「想定外の要因」が数多く発生していることが実情とも思われます。
以下に予見可能な危険要因について述べます。
2.1ワイヤロープ切断
ワイヤロープが切断した場合の防止策は,ライフライン(人の落下防止用ロープ)を垂らす以外は,ゴンドラの昇降装置で対策することは不可能です。その為にゴンドラ構造規格では,ワイヤロープ強度は10倍以上の安全率を設ける基準となっています。
ゴンドラが世に多く出始めた昭和40年代ころには,ワイヤロープ切断による事故が数例有ったことを先輩諸氏から聞いたことがあります。
昭和44年のゴンドラ構造規格の公示に始まり諸法令化されたことにより,各メーカーでも様々な安全対策の実施,事業主による定期点検の実施,使用者による始業点検の徹底等で,常設型ゴンドラでは起こりえない要因となっています。
2.2減速機出力軸の破断
減速機出力軸が破断した場合は,ワイヤードラムが空転状態となり,作業床は落下します。この軸が破断する原因としては以下が想定されます。
- 芯出し不良による軸の疲労破壊
- 取付ボルトの締め不足により,芯ずれが発生し軸が疲労破壊する
- 軸強度不足による軸の破断
これらの危険要因の全ては設計,製造,品質管理の徹底で回避出来ます。
弊社では検査会社の協力を得て,実際の減速機出力軸に「ひずみゲージ」を組み込んだ減速機を使用して,作業床を吊った運転中に軸に作用する「曲げ応力」と「ねじれ応力」の実測値を測定する実験を行いました。
この実験により計算式で得られる値と実際に発生する値の整合性の確認を行い,その結果を元に以下の事項を確立しました。
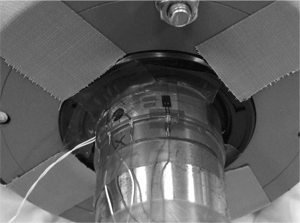 |
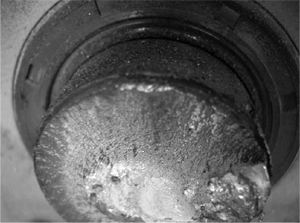 |
写真
1 軸に組込んだひずみゲージ |
写真
2 実験にて疲労破断させた軸 |
2.3減速機入力軸の破断
減速機入力軸が破断した場合は,ワイヤードラムが空転状態となり,作業床は落下します。この軸が破断する原因としては以下が想定されます。
- 芯出し不良による軸の疲労破壊
- 電源の逆相運転により,負荷が拘束された状態で回転しようとすることにより発生する軸のねじれせん断
これらの危険要因全ては製造,品質管理,定期点検の徹底で回避出来ます。
2.4減速機油の異常
減速機油に異常が発生した場合は,減速機内部の破壊を招き,ワイヤードラムが空転状態となり,作業床は落下する場合があります。異常となる原因として以下が想定されます。
- 異物が混入し,ギア面が磨耗し破損に至る
- 定期交換しないまま使用し,油の劣化によりギア面が磨耗し破損に至る
- 外気温度に適さない粘性の油により,潤滑油の効果が著しく落ち,ギア面が磨耗し破損に至る
これらの危険要因の全ては,定期点検の徹底で回避出来ます。
弊社では,「もし油交換を忘れていたら」のリスクに対して,減速機許容トルクの約80%相当の荷重を吊った実験装置を用いて連続運転し,一定時間毎に減速機内部の変化を目視調査行いました。
一般的なウオーム減速機では油交換は初回が100時間以内,2回目以降は500時間毎となっています。
500hrs: |
ウオームホイール(BC材)の切粉が多数油に混入。油粘度は若干低下しており,油色は黄色からうす茶色く変色。ギア歯面に異常は無い。 |
1000hrs: |
油粘度は逆に高くなり若干硬い状態となる。油色は濃い茶色となり,切粉の判断が出来ないほど濃い色となる。歯面は全体的に浅い傷が発生していた。 |
1500hrs: |
油はグリス状に硬化し,ほぼ黒色となる。歯面はモジュールに対して10%以上の磨耗が発生し,部分的に欠損も生じていた。 |
1900hrs: |
運転中に異音が度々発生し,減速機ケース表面温度が80℃を超える。焦げつく異臭も発生する。歯面は30%近くまで磨耗する。 |
2175hrs: |
吊っていた物が約30センチ程落下し減速機は回転不能となる。ギア歯が6枚せん断し,他の歯面も50%近く磨耗していた。 |
減速機の耐用期間は一般的には25000時間(一部機種は15000時間)で設計されています。
この耐用期間はあくまでも定期的な油交換及び部品交換を行い,定期的なメンテナンスを行った上での期間です。ゴンドラの場合は使用頻度もまちまちな上,設置環境が良くない傾向にあるため,一般的な耐用期間よりは短く設定しています。実験結果を元に以下の事項を確立しました。
- 昇降累計運転時間計の設置
- 合成油が使用出来る減速機の採用
(「合成油」は実験に使用した「鉱物油」より温度変化に対する粘度変化が少ないため)
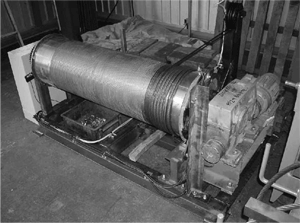 |
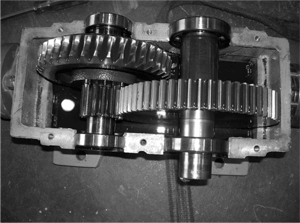 |
写真
3 実験装置外観 |
写真
4 減速機内部 |
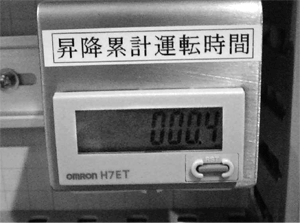 |
写真
5 昇降累計運転時間計 |
2.5全ブレーキの無効化
「全ブレーキの無効化」とは,ブレーキ全てが制動力を失った場合を意味します。
ゴンドラ構造規格第21条に「制動トルクの総和は …1.5倍以上」と明記されており,常設ゴンドラのほぼ全てにおいて,昇降用ブレーキは2台以上設置されており,制動トルクも1.5倍以上確保されています。2台のブレーキが同時に制動力を失うことは,確率的にはかなり低い要因となります。
ゴンドラに採用されているブレーキの全ては給電が遮断されればバネにより制動力を確保しており,ブレーキが故障した場合は制動力が維持されます。
しかしながら,以下の原因などではブレーキの制動力が失われることが想定されます。
- ライニング板の異常磨耗
- ブレーキ機構への油脂の混入
これらの危険要因の全ては,定期点検の徹底で回避出来ます。また,昇降装置の多くは「ウオーム減速機」を採用しており,減速機のセルフロック効果によって万が一にブレーキが無効化しても,作業床の自由落下は起こりません。
弊社の実験では,下降速度より若干早めの速度でスルスルと落下することを確認しています。(減速機サイズや吊り下げ荷重によって相違があります。)
2.6ドラム軸キーせん断
ドラムと軸の接合部分における「キー」がせん断した場合は,ワイヤードラムがフリー状態となり,作業床は落下します。キーが破断する原因としては以下が想定されます。
- キー強度不足
- 繰り返しによるキー疲労せん断
- キーのはめ合い公差不良
これらの危険要因の全ては設計,製造,品質管理の徹底で回避出来ます。
|